CNC (Computer Numerical Control) machine shops are essential in modern manufacturing. They offer precise machining services for various industries, from automotive to aerospace and electronics. While CNC machining delivers high-quality parts, optimizing production time and costs is crucial for both the CNC shop and its customers.
In this blog, we will explore how CNC machine shops reduce production time and lower costs while maintaining quality. Understanding these strategies can help businesses make better decisions when choosing a CNC machine shop for their needs.
What is a CNC Machine Shop?
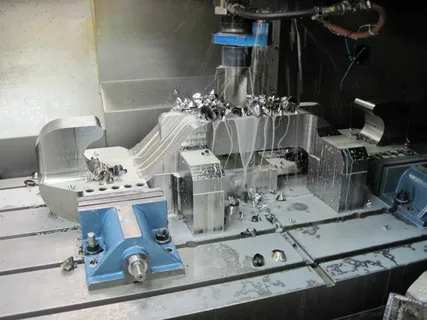
What Do CNC Machine Shops Do?
A CNC machine shop is a facility that uses computer-controlled machines to create parts from various materials, such as metal, plastic, and wood. CNC machines work with extreme precision, making them ideal for industries that require high-quality parts.
CNC machines include lathes, milling machines, routers, and grinders. These machines are programmed using specialized software to cut, shape, or drill materials to create the desired part.
Who Uses CNC Machine Shops?
CNC machine shops serve many industries, including:
- Automotive: Producing parts like engine components and gears.
- Aerospace: Manufacturing aircraft parts with tight tolerances.
- Medical: Creating medical devices and surgical tools.
- Electronics: Making small, detailed components for electronic devices.
- Consumer goods: Producing parts for various household products.
Now, letβs dive into how these CNC machine shops optimize their processes to save time and reduce costs.
How CNC Machine Shops Optimize Production Time
1. Efficient Machine Programming
One of the key ways CNC machine shops speed up production is through efficient machine programming. Every CNC machine operates based on a program that tells it how to move and cut the material. The better the program, the less time the machine spends making errors or unnecessary moves.
Streamlined Programs
By refining these programs and eliminating unnecessary steps, CNC machine shops reduce the amount of time a machine spends running. This directly leads to faster production times and ensures parts are made quicker without compromising quality.
Advanced Software
Many CNC machine shops use advanced software for programming. This software allows for precise instructions, faster programming times, and the ability to test programs in a virtual environment before using them on actual materials. This avoids costly mistakes and cuts down on trial-and-error programming.
2. Using High-Speed Machining Techniques
High-speed machining (HSM) is another method CNC machine shops use to optimize production time. HSM involves using faster spindle speeds and quicker cutting feeds. This allows the machine to remove material more rapidly without sacrificing precision.
Why Use High-Speed Machining?
High-speed machining reduces the time spent on each part by cutting faster and making fewer passes over the material. This means that more parts can be made in a shorter amount of time.
HSM is particularly useful when working with softer materials like aluminum or plastic, where faster cutting speeds donβt affect the partβs integrity.
3. Reducing Setup Time
Setup time refers to the time spent preparing the machine and materials before the actual machining process begins. This includes loading tools, clamping the material, and programming the machine.
Modular Fixtures
Many CNC machine shops use modular fixtures to reduce setup time. These fixtures allow the shop to quickly switch between different parts and setups, minimizing the time it takes to change from one job to another.
Automated Tool Changing
Automated tool changers (ATC) are another way shops reduce setup time. These systems automatically switch tools during the machining process, saving the operator from manually changing them. This increases efficiency and reduces the chances of human error.
4. Minimizing Machine Downtime
Machine downtime refers to any time when a machine is not running. This can happen for various reasons, such as maintenance, tool changes, or programming issues. CNC machine shops strive to minimize downtime to keep production running smoothly.
Preventive Maintenance
One way CNC shops reduce downtime is through preventive maintenance. By regularly checking and servicing machines, they avoid unexpected breakdowns that could halt production. This keeps the machines running at their best and reduces the risk of costly repairs or delays.
Tool Monitoring Systems
Tool monitoring systems track the condition of tools used in the machining process. These systems alert the operator when a tool is worn out or about to break, allowing for timely replacement before it affects production.
How CNC Machine Shops Reduce Costs
1. Optimizing Material Use
One of the main costs in CNC machining is the material used. By optimizing how materials are used, CNC machine shops can significantly reduce waste and lower costs for their customers.
Nesting Techniques
Nesting refers to arranging multiple parts in the most efficient way on a sheet of material. CNC machine shops use nesting techniques to minimize waste, ensuring that as much material as possible is used. This reduces the cost of materials and also helps with environmental sustainability.
Choosing the Right Material
CNC machine shops also help customers choose the right material for their parts. By selecting materials that are easier to machine or have a lower cost, shops can reduce the overall cost of the project without sacrificing quality.
2. Investing in Advanced Machines
Although advanced CNC machines can be expensive upfront, they offer long-term cost savings. These machines are faster, more precise, and more efficient than older models. This means they can produce parts more quickly, reducing labor costs and the time spent on each project.
Multi-Axis Machines
Multi-axis CNC machines allow for more complex parts to be made in a single setup. This eliminates the need for multiple machines or setups, reducing the overall time and labor needed for production.
3. Batch Production and Automation
CNC machine shops often produce parts in batches to save time and lower costs. Batch production allows for more efficient use of materials, machines, and labor.
Automation
Automation plays a huge role in reducing costs. Many CNC machine shops use automated systems to handle repetitive tasks, such as loading and unloading parts. This reduces the need for manual labor, which lowers labor costs and increases efficiency.
4. Outsourcing Non-Core Processes
To keep costs low, some CNC machine shops outsource non-core processes like finishing, painting, or assembly to specialized companies. This allows them to focus on machining while leaving other tasks to experts who can perform them more efficiently and at a lower cost.
Why Outsource?
By outsourcing these tasks, CNC machine shops can avoid the cost of investing in additional equipment and training for these non-core processes. This helps reduce overhead costs and ensures that the customer gets a high-quality finished product at a lower price.
5. Using Lean Manufacturing Principles
Lean manufacturing is a methodology that focuses on reducing waste and improving efficiency. Many CNC machine shops implement lean principles to optimize their operations and reduce costs.
Eliminating Waste
Lean manufacturing involves identifying and eliminating waste in the production process. This can include unnecessary steps, excess materials, or inefficient workflows. By streamlining operations, CNC machine shops can lower costs and improve production speed.
Continuous Improvement
Lean manufacturing also encourages continuous improvement. CNC machine shops regularly review their processes and look for ways to improve efficiency, reduce waste, and lower costs. This ensures that they are always working to provide the best value to their customers.
Conclusion
CNC machine shops play a vital role in the manufacturing world. By optimizing production time and costs, they can deliver high-quality parts quickly and at a competitive price. Through efficient programming, high-speed machining, reducing setup time, and minimizing downtime, they save time and money for both themselves and their customers.
Additionally, by focusing on material optimization, investing in advanced machines, batch production, outsourcing, and lean manufacturing, CNC machine shops reduce costs without sacrificing quality.
Whether youβre looking to produce a single prototype or need mass production, understanding how CNC machine shops operate can help you make informed decisions and get the best results for your project.
Choosing the right CNC machine shop that uses these cost-saving and time-optimizing techniques can lead to smoother operations, faster delivery times, and lower overall costs for your manufacturing needs.
For more insightful articles related to this topic, feel free to visit digiglowseo.co.uk